
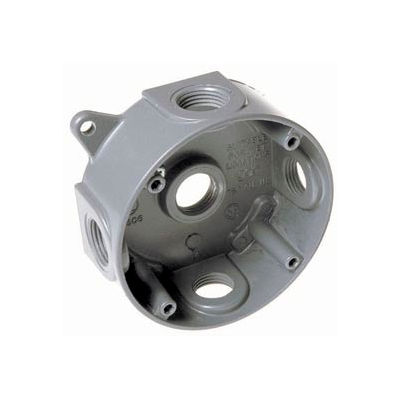
With over 30 years of experience offering advanced network solutions-including our revolutionary gel sealing technology-CommScope can help your network realize its full potential today and tomorrow. By knowing where in the outside plant FTTx network you’re building, finding an easy-to-deploy and long-lasting closure becomes effortless with CommScope’s proven (yet future focused) fiber closure family. Distribution and drop network solutionsįor example, as you move closer to the customer, frequent re-entry access is essential-whereas, in the trunk network, a fit-and-forget solution is often the preferred option.Feeder and distribution network solutions.To choose the right fiber splicing closure, you must determine which solution best suits your needs in the specific part of the network: gschmidt958 has updated the project titled OP Amps Gone Digital - A BCD to 7 Seg Converter.To tackle the variety of challenges service operators face when deploying fiber, CommScope has created a family of fiber optic splice closures that balance key criteria such as reliability, installability, flexibility and speed of deployment.Ahron Wayne has updated the log for X-Ray CT scanner gets new life.100dollarhacker has updated the log for AFM - from ground up.gschmidt958 has updated details to OP Amps Gone Digital - A BCD to 7 Seg Converter.RW ver 0.0.3 on Navy Program PUMPs Up Hopes For Magnetic Propulsion.PEBKAC on Victorian Train Tunnel Turned Test Track.oneguythought on Increasing System Memory With The Flick Of A Switch.Piecutter on Op Amp Contest: Generate Spirograph Shapes Using Only Op Amps And Math.Thomas Hargrave on Op Amp Contest: Generate Spirograph Shapes Using Only Op Amps And Math.Around 37 percent of the world’s annual oil. Oil and gas drilling extracts the fuel that powers everything from automobiles to the heat in our homes. From energy to food production to landscaping, each is an important part of our world today. The Commenter Formerly Known As Ren on The Printing Of Pi Here are six applications that commonly require submersible junction boxes.Isaac on Op Amp Contest: Generate Spirograph Shapes Using Only Op Amps And Math.The Commenter Formerly Known As Ren on Victorian Train Tunnel Turned Test Track.The Commenter Formerly Known As Ren on Op Amp Contest: Generate Spirograph Shapes Using Only Op Amps And Math.Hackaday Podcast 221: The Future Of The Raspberry Pi, Sniffing A Toothbrush, Your Tactical Tool Threshold 1 Comment Use inhibitor at joins, and where safety matters, have an exposed ground. But ask any electrician who’s ever dug one of these things up. It really could be waterproof, in principle. A common technology for buried wires is to put them in a bit of PVC conduit, it’s almost the same stuff as pressurized water pipes. I know that you cant bury splices and they need to be accessible, but what if there are no splices. If you want to seal it, use a pressure fitting, a rubber washer actually compressed between the wire’s insulation and the box. Circuit 2 is for my soon to be built outdoor BBQ. If you have a flexible caulk up against a wire’s insulation, even thermal cycling will cause the two to separate. It’ll be fine for years and years, a lot longer than this plastic will last. First off, you don’t need this much effort - unless you’re actually going to bury the thing, just use a metal box with a grounded outside, and put inhibitor on the connections. Posted in how-to, Tool Hacks Tagged 3d printed, enclosure, junction box, oogoo, sealant, silicone Post navigation The resulting mixture will be thicker, but it’ll cure throughout with no problems. If that will be a problem, maybe take a cue from Oogoo and mix in a bit of corn starch with the silicone sealant. A thick gob of the stuff will tend to firm up on the outside but leave the inside gooey. One thing to keep in mind about silicone-based sealants is that thick gobs of it can take a really, really long time to cure fully.
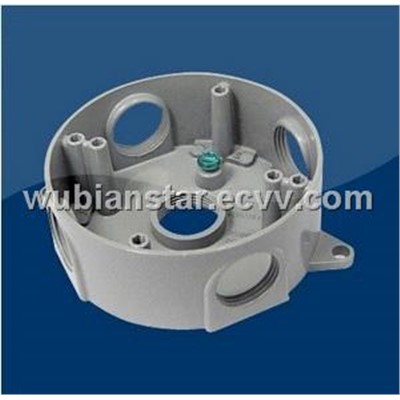
There are also 3D printed nozzles in a variety of designs. For tubes of sealant that have threaded tops, one can more effectively save the contents of the tube for later with this design for screw-on caps. has a couple of companion designs, as well. Afterwards, all there is to do is wait until the sealant cures.
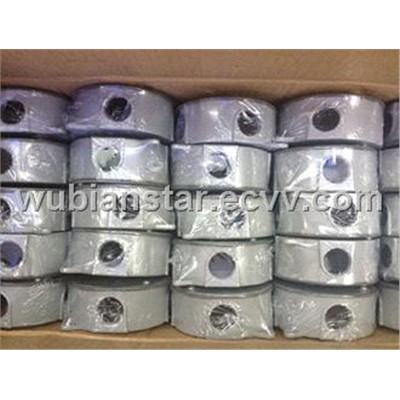
Sealant is then pumped in via the hole on the side, then the hole is plugged. The way it works is this: wires go through end caps which snap onto the main body, holding the junction inside. On the upside, it’s cheap, accessible, and easily customized. It’s also a one-way trip, because the result is sealed up like a pharaoh’s tomb. It’s a cross between an enclosure and potted electronics. Thingiverse user shared a design for 3D printed enclosures that are made to house wire and cable junctions, which can then be rendered weatherproof by injecting them with a suitable caulking compound and allowing it to cure.
